cas client
Rationalisation des diversités de produits dans un groupe automobile
1 | Contexte et problématique du client
Notre client, un groupe automobile majeur en Europe, a été formé suite à l’acquisition de deux concurrents au cours des 20 dernières années.
Malgré cette croissance externe, le groupe fait face à des défis structurels importants. Actuellement, il produit une large gamme de véhicules dans 16 usines différentes, couvrant presque tous les segments du marché. Cette offre va des véhicules urbains aux modèles routiers, des solutions économiques aux véhicules premium. Cependant, ce vaste portefeuille et la dispersion géographique des sites de production génèrent des complexités.
Un manque de synergies entre les entités historiques du groupe.
L’un des principaux problèmes identifiés est la très faible intégration des différentes entités acquises. Depuis les acquisitions, peu d’efforts ont été faits pour mutualiser les informations, les composants ou même les méthodes de travail entre les anciennes structures et les nouveaux membres du groupe. Chaque entité fonctionne presque comme une organisation distincte, avec ses propres processus, ce qui entraîne une inefficacité opérationnelle et un manque de cohérence dans la chaîne de valeur.
Résultat : des pertes financières et un échec dans la mise en place d’un projet PLM.
En 2015, notre client a enregistré des pertes financières historiques, en partie dues à l’absence de synergies internes. De plus, une tentative de mise en place d’un système de gestion du cycle de vie des produits (PLM) s’est avérée infructueuse, soulignant les difficultés du groupe à centraliser et harmoniser ses opérations. Cette situation empêche le groupe de pleinement tirer parti de son potentiel, tant en termes de réduction des coûts que d’optimisation des processus.
Problématique : Comment harmoniser les diversités de produits et rationaliser les processus internes au sein de ce groupe automobile pour améliorer l’efficacité opérationnelle et restaurer la rentabilité ?
2 | Notre approche
Pour accompagner notre client dans sa transformation, il est crucial d’adopter une approche structurée. Cela inclut l’analyse de l’architecture existante, l’identification des améliorations nécessaires et la définition de pratiques communes. Cette démarche facilitera la gestion des projets futurs et renforcera l’efficacité opérationnelle. Voici les grandes parties de cette approche :
1 | Diagnostic initial et cadrage organisationnel
Notre approche a débuté par une transformation vers l’ingénierie système à l’aide d’une méthodologie « middle-out ». Cette approche consiste à partir du cœur de l’organisation, en identifiant d’abord les points de synergie potentiels, puis en les déployant à travers les différentes entités. La première étape a été un cadrage de l’organisation, visant à comprendre en profondeur les processus existants, les structures des trois marques historiques, et à identifier les sources de fragmentation.
2 | Définition d’une architecture véhicule générique et de standards communs
Nous avons ensuite travaillé à la création d’une architecture véhicule générique et d’un cahier des charges commun à l’ensemble des trois marques historiques du groupe. L’objectif était de rationaliser les produits et de faciliter les échanges entre les entités. Cela comprenait également l’identification de standards de conception communs, afin de réduire la redondance et les variations inutiles dans le processus de développement.
3 | Mise en place d’un nouveau plan de développement orienté ingénierie système
Une fois l’architecture générique définie, nous avons élaboré un nouveau plan de développement basé sur les principes de l’ingénierie système. Ce plan a été conçu pour être en adéquation avec l’architecture commune, permettant ainsi une gestion plus centralisée et harmonisée des projets de développement au sein du groupe. Une nouvelle organisation a également été mise en place, alignée sur cette stratégie, pour garantir une meilleure collaboration entre les équipes des différentes marques.
4 | Restructuration du système PLM sur la base de la nouvelle organisation
Enfin, nous avons restructuré le système PLM (gestion du cycle de vie des produits) pour qu’il soit en phase avec la nouvelle organisation, le plan de développement et l’architecture véhicule générique. Le PLM a ainsi été optimisé pour soutenir l’intégration des processus et faciliter la gestion des données produits à travers les différentes entités du groupe, créant une véritable continuité numérique.
Cette approche a permis de poser les bases d’une transformation en profondeur, visant à rationaliser la diversité des produits et à optimiser l’efficacité opérationnelle du groupe.
Exemples de livrables :
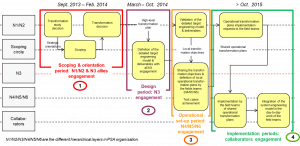
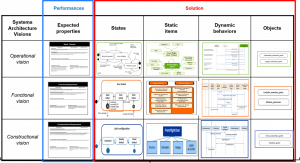
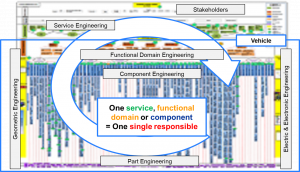
3 | Résultats et bénéfices de la mission
Notre intervention a permis au groupe automobile de réaliser une transformation profonde avec des résultats concrets. En créant des vues architecturales unifiées, nous avons aidé à instaurer une vision partagée des synergies entre les marques et à améliorer la coordination. La définition des fonctionnalités du nouveau PLM a également permis de mieux structurer le développement des produits.
Les résultats clés incluent :
— Réduction de 14 % du temps de gestion des exigences
— Diminution de 7 % du temps de test
— 85 % des exigences connectées à des tests en 2016 (vs. 45 % au départ)
Ces améliorations ont permis de réduire les coûts, d’augmenter la productivité et d’optimiser les processus, renforçant ainsi la compétitivité du groupe sur le marché.